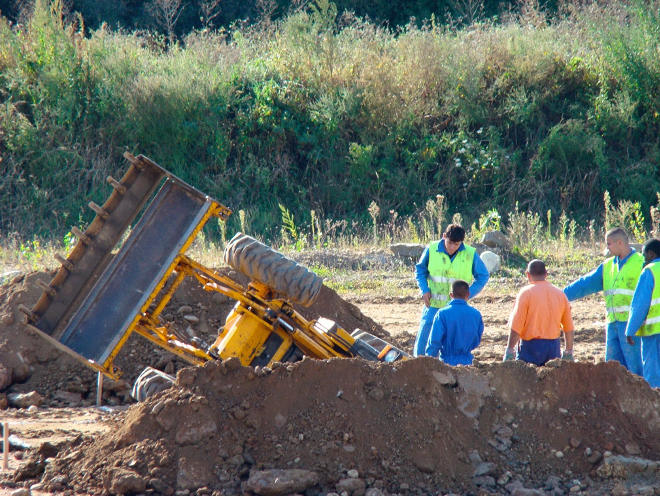
One of the major benefits of incorporating digital technology into the control of construction worksites is a higher standard of safety and security for workers. Thankfully, there have already been big improvements in safeguarding worker safety in recent years due to greater awareness and tighter regulations, but there are now opportunities to take this even further using digital innovations.
Construction sites can be very dangerous places. According to Eurostat, 20.6% of all fatal accidents at work in the EU-28 during 2017 occurred within the construction sector. There are hazardous situations everywhere you look – from electricity and moving vehicles to slips, trips and falls from height, to name but a few.
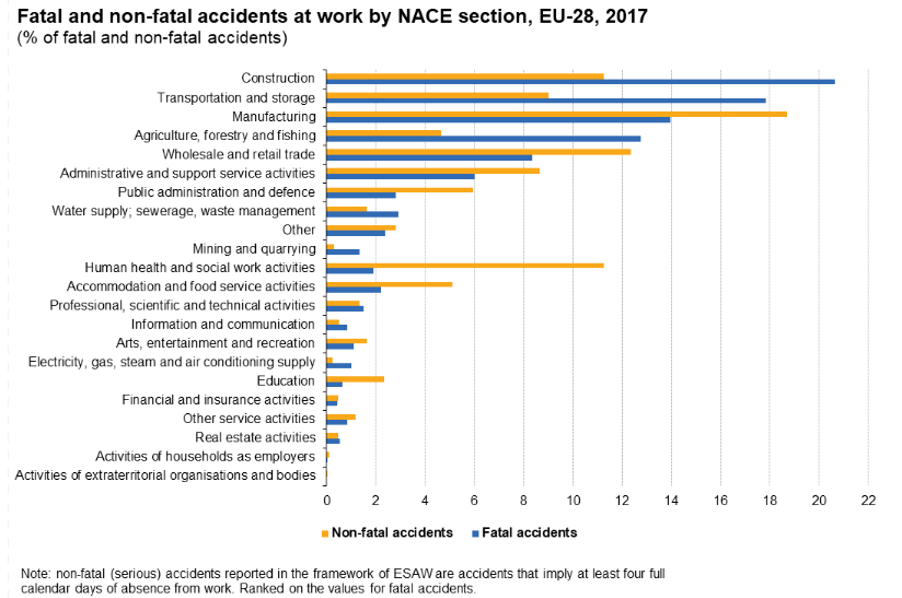
[Source: Eurostat]
The consequences of accidents can range all the way from a minor injury to a fatality. Apart from this potentially catastrophic human cost, there are also other costs to the company in terms of lost productivity and significant legal and insurance expenses.
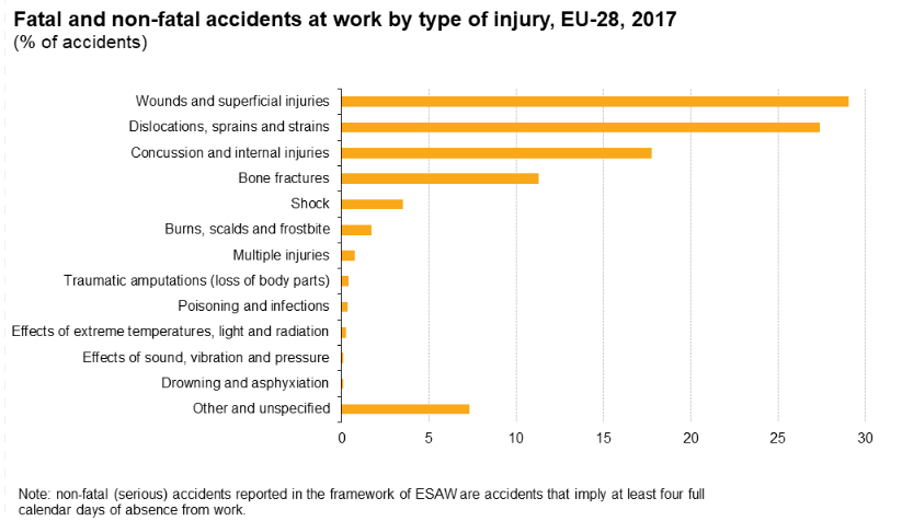
[Source: Eurostat]
Conventional ways to reduce accidents
The construction industry has made great strides in managing and reducing these hazards in recent years. All companies should be aware of best practices to avoid accidents on-site, such as providing safety training, wearing the correct PPE and developing risk assessments. This can even extend to possibly less well-known aspects of accident prevention, such as reducing the amount of night work, avoiding sunlight to reduce fatigue and encouraging healthy eating.
But there is still always room for improvement. Anyone who has had to work with a lengthy risk assessment document or complete a permit-to-work form on a large site, for example, will be aware of the limitations of using paper. There is huge scope for human error and it can be very difficult and time-consuming to gather and analyse the data. This is why digital tools are so valuable and can take safety to the next level.
The benefits of digital tech
Digital tools are now being used to replace traditional pen and paper, and even spreadsheets etc, for managing site safety and security in an increasing number of industries, with construction being one of these. The advantages of digital tech over traditional methods of data gathering and processing include:
- Better organisation and management of recurring safety training and meetings. A worker’s digital administrative profile can be created, where every time that a worker completes training or attends a meeting it is recorded in a central platform. This allows the HSE manager and HR department to better manage the administrative status of their staff and also of external workers, such as subcontractors.
- Improved crisis management – for example, by utilising device location (GPS). If all workers are equipped with a smartphone, they will be able to quickly and accurately notify the relevant people of the exact location of an incident, leading to a better response.
- Control the use of equipment and tools used on-site. It is important to keep track of the equipment that is brought onto site and also when it is removed. Thefts from worksites are still common and thieves are only too willing to exploit any flaws in security. In addition to deterring theft, the scheduling of planned maintenance is easier with the digital management of equipment. Furthermore, this enhanced level of control can also be used for managing equipment stored off-site, such as in warehouses.
- Ensure that all your workers and subcontractors are administratively eligible for work, with daily check-ins on-site. For example, by implementing a badge reader that is directly connected to a central platform, the administrative status of a worker can be verified automatically. This means managing the required accreditations, driving permits, health and safety training, and other documentation of your workers and subcontractors to ensure their administrative compliance.
- Make sure workers use the correct PPE for hazardous tasks. For example, one way to control this is by installing site cameras in strategic areas, such as at the entrance, on a crane or at the delivery area.
- Intelligently manage vehicle movements using geolocation. This can include timing deliveries etc to make sure that there are not too many vehicles on-site at any one time. This can also help with following vehicle maintenance plans defined by mileage, automatically identifying the driver(s) for recording of hours and increased responsiveness through automatically generated alerts according to your work regulations (e.g. speed limits).
- Proactive decision making is made easier. Rather than being reactive and sometimes delayed by days or even weeks, insights that come from connected objects and wearables collecting real-time data for all mobile resources on-site will allow much more proactive – and therefore better – decision making and resource management.
Protecting your reputation
A vital component of the long-term success of any company is its reputation. A poor health and safety record will be not only financially damaging to a company but also potentially disastrous to its reputation. As there are digital tools available now that can significantly enhance the management of health and safety on-site, there is a very strong economic and strategic argument in favour of using them. Digital tools represent a very valuable opportunity that shouldn’t be missed.