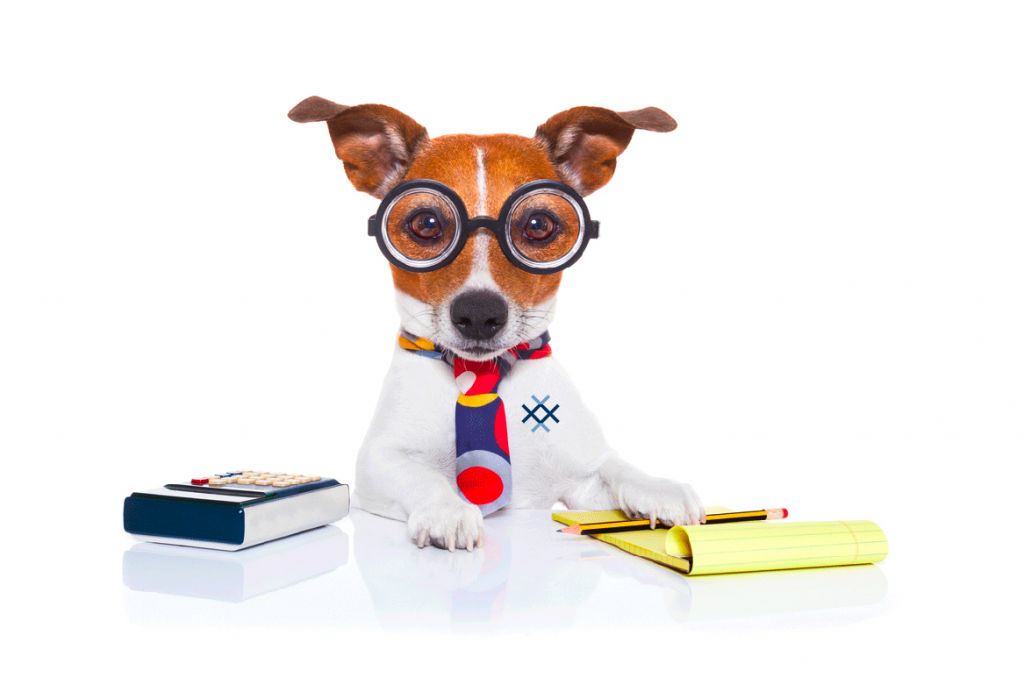
Calculating an accurate – but still competitive – costing for a construction project can be a very difficult task. Often, due to the large scale of a project and the quantities of labour, materials and equipment involved, not to mention the added complexities with bringing in numerous subcontractors, working out a construction cost can sometimes feel like a journey into the unknown. Digital tools can make this process significantly easier by providing good quality data about construction labour costs and also time and material costs to input into the calculations and also by crunching the numbers for you. This is just one feature of using digital tools to better control construction projects.
One aspect of calculating the total cost for a bid that can cause particular problems relates to the cost of the labour that is used on the project. But it is vital for the financial success of a project to get this right because the cost of labour makes up such a significant part of the total cost. According to The Construction Labor Market Analyzer, your construction labour cost percentage should be anywhere from 20% to 40% of total costs.
Terminology in this area can vary slightly from country to country and the specific costings that are required will vary from project to project (for example, the labour burden as a percentage or as an hourly cost). But the descriptions below give an overview of the sorts of calculations that are necessary to establish your labour costs.
Direct and indirect labour costs
The cost of your labour force is made up of two distinct elements: direct costs and indirect costs. Direct costs are the wages that you pay to your workers – this is sometimes also called the base rate. Indirect costs relate the cost of each employee outside of their hourly wage. This includes things like payroll taxes, insurance, holiday and sickness pay, training and other employee benefits.
The labour burden is the cumulative total of these direct and indirect costs. It is also sometimes given as a percentage:
Labour burden (%) = Indirect costs / direct costs * 100
In addition, the labour burden can be expressed as an hourly cost by dividing the total yearly labour cost by the number of hours an employee will work. For example:
An 8-hour working day over 52 weeks = 8 hrs x 5 days x 52 weeks = 2080 hrs
A 20-day holiday allowance and predicted absences (sickness, training, etc) of 25 days per year = 20 days + 25 days = 45 days (45 days x 8 hrs = 360 hrs)
Total workable hours = 2080 hrs – 360 hrs = 1720 hrs
If the annual labour burden comprises the following:
Payroll taxes = £3000
Insurance = £1000
Employee benefits = £2000
Other expenses = £3000
Total annual labour burden = £3000 + £1000 + £2000 + £3000 = £9000 Converting this total annual labour burden to an hourly cost is done by: Total annual labour burden / total workable hours = £9000 / 1720 hrs = £5.23
Values are usually rounded up to allow for a margin of error and to simplify calculations. The labour rate that eventually feeds into your project cost calculation comes from the labour burden along with the mark-up that is required to provide a profit for your company.
Unit times and yield
Of course, knowing the cost of your labour is only half of the problem: you also need to know how much labour will be needed to complete the task. For this, a unit time is sometimes used – for example, it might take 0.5 hour to build 1m2 of brick wall. For a 100m2 brick wall, the unit time will be 50 hours.
If the work is performed by a team of five workers, the execution time is 50 hrs / 5 people = 10 hrs.
The yield indicates the quantity of units of work carried out in a period, usually an hour or a day. This is used to establish the potential work of the labour force or equipment and determines the duration that the labour, for example, is needed for. The duration is calculated by dividing the quantity of work by the yield – for example, a 50m2 brick wall is to be built at a yield of 16m2 per day:
Duration = quantity of work to be carried out / yield = 50m2 / 16m2 per day = 3.125 days
Unit times and returns are calculated either by using experience gained on other similar projects or, when this isn’t possible, by deduction and analysis using research and logical reasoning.
How digital tools can help to accurately calculate labour costs
All of these calculations rely on one thing: good data. After all, the old saying goes that if you put garbage in, you get garbage out. This is where a tool such as a digital timesheet becomes invaluable. This time-tracking app allows your workers to easily record their jobs, work hours, any absences and other relevant information that is required by payroll. Aside from providing data that is more accurate and less prone to errors than traditional paper-based documents or spreadsheets, digital timesheets enable live and integrated data tracking. They also greatly increase the level of precision in the data because workers are able to assign hours to a specific task or workstation.
Digital timesheets using time and material software are directly accessible on smartphones, tablets and a web portal, collecting data that is required for payroll management and the tracking of submissions (finance code, submission category code, cost structure, etc). Key features of digital timesheets include:
- A streamlined process for collecting, analysing, monitoring and integrating field data.
- Offline mode for optimal and uninterrupted usage on-site.
- A signature-approval function adapted to your current process.
- Personalised content adapted to your own payroll process.
- Pre-population of hours and days taken from the schedule or previous days.
- The easy addition of new workers and copying of repetitive activities.
Calculating labour costs accurately is crucial
The bottom line here is that a construction company will struggle to remain competitive and financially viable if it doesn’t have a good knowledge of its labour costs – how can you charge someone a realistic fee if you don’t know how much it is going to cost you to do the work? Providing a bid that has significantly over- or under-estimated labour costs will not be good for business, to put it mildly. To avoid this scenario, labour cost data that is accurate and has the required level of detail is needed. Digital timesheets can help to provide this vital data and ensure that your company produces competitive, yet still profitable, bids.